علت افت فشار دستگاه تزریق پلاستیک
علت افت فشار دستگاه تزریق پلاستیک
دستگاه تزریق پلاستیک بهترین گزینه به منظور تولید مقادیر بسیار زیاد قطعات پلاستیکی است از این رو انواع مختلفی از دستگاههای تزریق پلاستیک و قالب سازی وجود دارد که برحسب نوع نیاز و نحوه کار تولید میگردد. از جمله کاربرد های این دستگاه میتوان به ساخت اسباب بازی ظروف پلاستیکی قاب گوشی و….. اشاره نمود . افت فشار در دستگاه تزریق پلاستیک یکی از مشکلات رایج و حیاتی است که می تواند به طور مستقیم بر کیفیت و کمیت تولید تأثیر بگذارد. درک دلایل این افت فشار برای هر اپراتور یا تکنسین دستگاه تزریق پلاستیک ضروری است. برای کسب اطلاعات بیشتر درباره ی کاربرد های این دستگاه و همچنین اطلاع از قیمت های دستگاه تزریق پلاستیک مانند قیمت خرید دستگاه ساخت قاب گوشی و ….. میتوانید از کارشناسان شرکت بولین که یکی از قدرتمندترین واردات دستگاه های تزریق پلاستیک است مشاوره بگیرید.
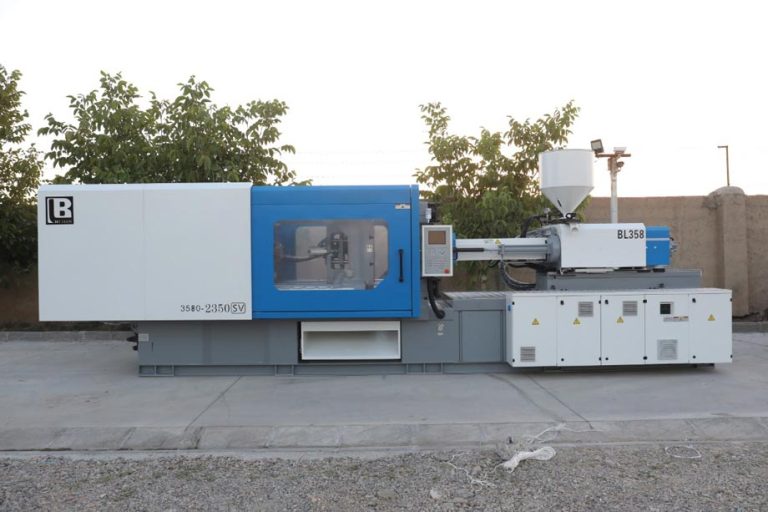
افت فشار در دستگاه تزریق پلاستیک: علل و راهکارها
افت فشار در دستگاه تزریق پلاستیک یکی از مشکلات رایج در صنایع تزریق پلاستیک است که می تواند بر کیفیت نهایی قطعات تولیدی تأثیر بگذارد و منجر به تولید قطعات ناقص یا دارای عیب شود. این پدیده می تواند به دلایل مختلفی رخ دهد از مشکلات مکانیکی و هیدرولیکی گرفته تا تنظیمات نادرست فرآیند و شرایط مواد. در این محتوا به دلایل اصلی افت فشار و همچنین راهکارهای پیشنهادی برای حل این مشکل می پردازیم تا بتوانید عملکرد دستگاه خود را بهبود بخشید.
بیشتر بخوانید: بهترین دستگاه تزریق پلاستیک سبد میوه
دلایل اصلی افت فشار در دستگاه تزریق پلاستیک
برای رفع مشکل افت فشار ابتدا باید علت اصلی آن را شناسایی کرد. دلایل متعددی می توانند منجر به کاهش فشار تزریق در دستگاه شوند که در ادامه به بررسی مهم ترین آن ها می پردازیم:
- کیفیت پایین قطعات هیدرولیکی
یکی از دلایل اصلی افت فشار در دستگاه تزریق پلاستیک استفاده از قطعات هیدرولیکی با کیفیت پایین یا فرسوده است. پمپ ها شیرها سیلندرها و آب بندهای هیدرولیکی نقش حیاتی در ایجاد و حفظ فشار مورد نیاز برای تزریق مذاب پلاستیک دارند. قطعات بی کیفیت یا مستهلک نمی توانند فشار لازم را به درستی تأمین یا کنترل کنند که نتیجه آن افت فشار در طول چرخه تزریق است. این مشکل به ویژه در سیستم های هیدرولیکی که تحت فشارهای بالا کار می کنند بیشتر نمایان می شود.
عدم رعایت اصول نگهداری: عدم تعویض به موقع روغن های هیدرولیکی یا فیلترها می تواند موجب خرابی و کاهش کارایی سیستم شود و در نتیجه فشار تزریق کاهش یابد. روغن هیدرولیک کثیف یا با ویسکوزیته نامناسب می تواند باعث سایش قطعات و کاهش راندمان پمپ شود که مستقیماً به افت فشار منجر می گردد.
2. مسدود شدن نازل یا مسیر جریان مذاب
مسدود شدن نازل تزریق یا هر قسمت دیگری از مسیر جریان پلاستیک مذاب (مانند اسپرو رانر یا گیت) به دلیل مواد باقی مانده مواد ناخالص یا خنک شدن پیش از موعد مواد می تواند منجر به افت فشار قابل توجهی شود. این انسداد مانند یک گلوگاه عمل کرده و مانع از عبور روان مواد با فشار کافی می شود. در نتیجه فشار در قسمت های قبل از انسداد بالا رفته و پس از آن به شدت افت می کند که این موضوع باعث می شود که مواد به صورت مناسب و با فشار کافی تزریق نشوند و کیفیت محصول نهایی تحت تأثیر قرار بگیرد.
3. مشکلات در سیستم کنترل دما (سیستم آب گرم کن هات رانر یا سیلندر)
سیستم کنترل دما چه مربوط به سیلندر دستگاه (بشکه) سیستم هات رانر قالب یا سیستم کنترل دمای قالب (که ممکن است با آب گرم کار کند) نقش مهمی در حفظ ویسکوزیته مناسب مواد تزریقی دارد. اگر این سیستم به درستی کار نکند و مواد به اندازه کافی گرم نشوند (یا بیش از حد گرم شوند و تخریب شوند) ویسکوزیته مواد پلاستیکی تغییر کرده و ممکن است به درستی ذوب نشده یا جریان نیابند. ویسکوزیته بالا به دلیل دمای پایین مقاومت در برابر جریان را افزایش داده و در نتیجه برای غلبه بر این مقاومت به فشار بیشتری نیاز است؛ اگر دستگاه نتواند این فشار را تأمین کند افت فشار رخ می دهد.
4. عدم تنظیم صحیح پارامترهای تزریق
تنظیمات نادرست فشار و سرعت در دستگاه تزریق پلاستیک نیز می تواند یکی از عوامل افت فشار باشد. هر ماده پلاستیکی و هر قطعه ای نیاز به پروفیل سرعت و فشار خاصی برای پر شدن صحیح قالب دارد. تنظیم سرعت تزریق بسیار بالا یا بسیار پایین تنظیم فشار نگهدارنده (Holding Pressure) نامناسب یا زمان ناکافی برای اعمال فشار نگهدارنده می تواند منجر به افت فشار در مراحل پایانی تزریق یا در مرحله نگهدارنده شود. تنظیمات نادرست می تواند منجر به عدم تأمین فشار مناسب و در نتیجه عدم تولید قطعات با کیفیت شود.
5. تماس با دیواره های قالب و طراحی نامناسب قالب
یکی دیگر از دلایل افت فشار مقاومت بیش از حد جریان مذاب در داخل حفره قالب است. این مقاومت می تواند به دلیل طراحی نامناسب قالب (مانند ضخامت کم دیواره ها طول زیاد مسیر جریان گیت های کوچک یا نامناسب) یا دمای نادرست قالب اتفاق بیفتد. دمای پایین قالب می تواند باعث خنک شدن سریع مواد در تماس با دیواره ها شود و ویسکوزیته سطحی مواد را افزایش دهد که این موضوع موجب افزایش ویسکوزیته و افت فشار در جریان تزریق شود. طراحی قالب باید به گونه ای باشد که امکان پر شدن کامل حفره با فشار معقول دستگاه فراهم شود.
6. خنک شدن سریع پلاستیک در مسیر جریان
خنک شدن سریع مواد پلاستیکی در حین فرآیند تزریق و قبل از پر شدن کامل حفره قالب باعث می شود که جریان مواد با فشار کافی ادامه پیدا نکند. این اتفاق معمولاً به دلیل تنظیم نادرست دمای سیلندر نازل هات رانر یا قالب یا سرعت تزریق بسیار پایین رخ می دهد. زمانی که مواد شروع به جامد شدن می کنند مقاومت در برابر جریان به شدت افزایش یافته و دستگاه برای غلبه بر این مقاومت با کمبود فشار مواجه می شود که منجر به افت فشار نهایی می گردد.
7. نقص در جک گالسه یا شیر آن
جک گالسه (Injection Cylinder) یا سیلندر تزریق و شیرهای هیدرولیکی مرتبط با آن نقش کلیدی در تأمین فشار لازم برای تزریق دارند. این سیلندر نیروی لازم را برای حرکت ماردون و تزریق مذاب به داخل قالب فراهم می کند. هر گونه نقص داخلی در سیلندر (مانند نشتی داخلی از پیستون یا آب بندها) یا خرابی در شیرهای کنترل کننده جریان روغن هیدرولیک به این سیلندر می تواند باعث کاهش فشار هیدرولیکی وارده به ماردون و در نتیجه افت فشار تزریق و مشکلات دیگر در فرآیند تزریق شود. بررسی دوره ای عملکرد این قطعات ضروری است.
8. نشت مواد هیدرولیکی یا مذاب پلاستیک
نشت مواد هیدرولیکی از اتصالات لوله ها شیلنگ ها یا آب بندهای سیستم هیدرولیک دستگاه نیز می تواند به افت فشار در کل سیستم منجر شود. نشتی روغن هیدرولیک به معنی از دست دادن سیال عامل فشار است و پمپ باید سخت تر کار کند تا فشار مورد نیاز را تأمین کند که در موارد شدید می تواند به افت فشار کلی سیستم و کاهش نیروی تزریق منجر شود. علاوه بر این نشت مواد مذاب پلاستیک از نازل خط جدایش قالب یا هات رانر نیز به معنی از دست دادن مواد و فشار در مسیر جریان است.
9. نارسایی در تنظیمات مراحل تزریق (شامل فشار نگهدارنده)
عدم تنظیم دقیق مراحل تزریق به ویژه فشار نگهدارنده (Holding Pressure) و زمان اعمال آن یکی از دلایل کلیدی افت فشار و مشکلاتی مانند شرینکیج (Shrinkage) در قطعه نهایی است. پس از مرحله پر کردن قالب فشار نگهدارنده برای جبران انقباض مواد در حین خنک شدن اعمال می شود. اگر این فشار ناکافی باشد یا زمان اعمال آن کوتاه باشد مواد کافی به داخل قالب تزریق نمی شود تا انقباض را جبران کند و این به صورت افت فشار در انتهای چرخه یا در قطعه نمایان می شود. اگر مراحل تزریق به درستی تنظیم نشده باشند دستگاه نمی تواند به صورت بهینه عمل کند و این باعث کاهش فشار در حین عملیات می شود.
راهکارهای پیشنهادی برای رفع افت فشار دستگاه تزریق پلاستیک
برای رفع مشکل افت فشار در دستگاه تزریق پلاستیک چندین راهکار و اقدام قابل انجام است که با بررسی دقیق علت اصلی می توانند به بهبود عملکرد دستگاه و افزایش کیفیت تولید کمک کنند. در ادامه به آن ها می پردازیم.
- استفاده از قطعات هیدرولیکی باکیفیت و نگهداری مناسب
یکی از مهم ترین راهکارها اطمینان از سلامت و کیفیت قطعات سیستم هیدرولیک است. استفاده از شیرهای هیدرولیکی پمپ ها سیلندرها و آب بندهای باکیفیت و مطابق با استانداردهای دستگاه می تواند پایداری فشار سیستم را تضمین کند. شیرهای هیدرولیکی نقش مهمی در تنظیم و کنترل جریان فشار در دستگاه تزریق پلاستیک دارند. تعویض قطعات فرسوده یا آسیب دیده با قطعات اصلی یا معادل های باکیفیت اولین گام در رفع مشکلات مربوط به افت فشار ناشی از سیستم هیدرولیک است.
رعایت اصول نگهداری: برای جلوگیری از افت فشار لازم است اصول نگهداری مانند تعویض به موقع فیلترهای هیدرولیکی و روغن ها رعایت شود. برنامه منظم نگهداری پیشگیرانه شامل بررسی سطح روغن کیفیت روغن تعویض فیلترها و بازرسی بصری قطعات هیدرولیکی می تواند از بسیاری از مشکلات مربوط به افت فشار جلوگیری کند.
2. تمیز کردن و بررسی مسیر جریان مذاب
نازل اسپرو رانرها و گیت های قالب باید به صورت دوره ای تمیز و بررسی شوند تا از مسدود شدن آن جلوگیری شود. مواد باقی مانده سوخته یا ناخالصی ها در این مسیرها می توانند باعث کاهش فشار در حین تزریق شوند. استفاده از مواد با کیفیت و بررسی منظم نازل و مسیرهای ورودی قالب به جلوگیری از این مشکل کمک می کند. در صورت مشاهده انسداد باید اقدام به پاکسازی کامل مسیرها نمود.
3. تنظیم صحیح سیستم کنترل دما
برای جلوگیری از افت فشار ناشی از مشکلات در سیستم کنترل دما لازم است دمای سیلندر نازل هات رانر و قالب به طور منظم بررسی و تنظیم شود. اطمینان از کارکرد صحیح المنت ها ترموکوپل ها و سیستم های خنک کننده و حفظ دمای مناسب مواد تزریقی بر اساس توصیه های سازنده مواد باعث می شود جریان مواد با ویسکوزیته مناسب و فشار کافی ادامه پیدا کند. کالیبراسیون دوره ای سنسورهای دما نیز توصیه می شود.
4. بررسی و تنظیم دقیق پارامترهای فرآیند
دقت در تنظیمات دستگاه تزریق پلاستیک یکی از کلیدهای جلوگیری از افت فشار است. تنظیم دقیق مراحل تزریق سرعت فشار زمان تزریق و فشار نگهدارنده بر اساس نوع ماده طراحی قطعه و قالب می تواند به بهبود عملکرد دستگاه و افزایش کیفیت قطعات تولیدی کمک کند. انجام مطالعات بهینه سازی فرآیند و استفاده از پروفیل های چند مرحله ای سرعت و فشار می تواند به غلبه بر مقاومت جریان و پر شدن کامل قالب کمک کند.
5. بررسی قالب و اصلاح طراحی یا دما
در صورتی که افت فشار به دلیل تماس غیرمطلوب مواد با دیواره های قالب یا محدودیت های طراحی قالب باشد لازم است قالب مورد بررسی قرار گیرد و در صورت امکان طراحی آن اصلاح شود (مثلاً افزایش سایز گیت رانر یا ضخامت دیواره در صورت امکان). تنظیم دمای مناسب قالب نیز در کاهش مقاومت جریان و حفظ فشار کافی در جریان تزریق بسیار مؤثر است. شبیه سازی جریان مذاب می تواند به شناسایی نقاط مشکل ساز در طراحی قالب کمک کند.
6. اطمینان از عدم مسدود بودن مسیرهای هیدرولیکی و مکانیکی
بررسی مسیر جریان مواد پلاستیکی و همچنین مسیرهای هیدرولیکی و اطمینان از عدم وجود مسدودی یا محدودیت در سیستم تزریق پلاستیک بسیار مهم است. مسدود شدن هر یک از مسیرها چه مسیر مذاب و چه مسیر روغن هیدرولیک می تواند به افت فشار منجر شود. همچنین بررسی مسیرهای هیدرولیکی و حذف هرگونه مانع یا مواد ناخالص در این مسیرها ضروری است. بررسی وضعیت مکانیکی ماردون و سیلندر نیز برای اطمینان از عدم ساییدگی یا آسیب که می تواند منجر به برگشت مذاب شود اهمیت دارد.
7. بررسی و تعویض قطعات هیدرولیکی فرسوده
قطعات هیدرولیکی دستگاه باید به طور دوره ای بررسی و در صورت نیاز تعویض شوند. آب بندها سوپاپ ها و سایر قطعات مستعد سایش باید به طور منظم چک شوند. استفاده از قطعات با کیفیت و حفظ اصول نگهداری دستگاه می تواند از نشت مواد و افت فشار جلوگیری کند. نشت داخلی در سیلندرها یا شیرها نیز می تواند باعث افت فشار شود که تشخیص آن نیاز به تست های تخصصی دارد.
8. تنظیم دقیق در مراحل سرعت و فشار تزریق
تنظیمات دقیق در مراحل سرعت و فشار دستگاه نیز به جلوگیری از افت فشار کمک می کند. باید اطمینان حاصل شود که دستگاه در هر مرحله از تزریق با سرعت و فشار مناسب کار می کند و هیچ ناهماهنگی در جریان تزریق وجود ندارد. استفاده از کنترل حلقه بسته (Closed-Loop Control) برای فشار و سرعت می تواند دقت و تکرارپذیری فرآیند را افزایش داده و نوسانات فشار را به حداقل برساند. تنظیم صحیح نقطه سوئیچ از سرعت به فشار نگهدارنده نیز حیاتی است.
سوالات متداول درباره افت فشار در دستگاه تزریق پلاستیک
افت فشار در دستگاه تزریق پلاستیک چه پیامدهایی دارد؟
افت فشار می تواند منجر به تولید قطعات ناقص (مانند شات های کوتاه یا Short Shots) قطعات دارای فرورفتگی (Sink Marks) کاهش ابعاد و وزن قطعه افزایش تنش های داخلی و در نهایت کاهش کیفیت و استحکام محصول نهایی شود.
بیشتر بخوانید: هر آنچه که درباره ظروف پت پلاستیکی باید بدانید!
چگونه می توان افت فشار را در حین فرآیند تشخیص داد؟
افت فشار معمولاً از طریق نمایشگرهای فشار روی دستگاه قابل مشاهده است. همچنین مشاهده علائمی مانند پر نشدن کامل قالب تغییر در ظاهر قطعات تولیدی (مثل شرینکیج یا فرورفتگی) یا افزایش زمان چرخه می تواند نشان دهنده وجود مشکل افت فشار باشد.
آیا نوع ماده پلاستیکی بر افت فشار تأثیرگذار است؟
بله ویسکوزیته و خواص جریان پذیری مواد پلاستیکی مختلف متفاوت است. مواد با ویسکوزیته بالا (مانند PC یا برخی ABSها) برای تزریق نیاز به فشار بیشتری دارند و بیشتر مستعد افت فشار در مسیرهای طولانی یا باریک هستند. انتخاب ماده مناسب و تنظیمات فرآیند مطابق با آن اهمیت دارد.
نقش فشار نگهدارنده در افت فشار چیست؟
فشار نگهدارنده پس از پر شدن اولیه قالب اعمال می شود و هدف آن جبران انقباض حجمی مواد در حین خنک شدن و اطمینان از ابعاد نهایی قطعه است. فشار نگهدارنده ناکافی یا زمان کم برای اعمال آن باعث می شود مواد کافی برای جبران انقباض وارد قالب نشود و نتیجه آن افت فشار در داخل قطعه و ایجاد شرینکیج است.
آیا دمای محیط کارگاه می تواند بر افت فشار سیستم هیدرولیک تأثیر بگذارد؟
بله دمای بیش از حد محیط می تواند باعث افزایش دمای روغن هیدرولیک شود. روغن داغ تر ویسکوزیته کمتری دارد و ممکن است منجر به افزایش نشت داخلی در پمپ ها و شیرها و در نتیجه کاهش راندمان و افت فشار شود.
این مشکل خیلی رایج به نظر میاد. خوشحالم که این مقاله رو پیدا کردم. حالا میدونم که چرا قالبهای من همیشه خوب پر نمیشن.
اطلاعات این مقاله خیلی ساده و روان توضیح داده شده. حتی من که زیاد از دستگاه تزریق سر در نمیارم، متوجه شدم که مشکل از کجاست.
فکر کنم یکی از دلایل افت فشار، کیفیت پایین مواد اولیه باشه. قبلا هم این مشکل رو تجربه کرده بودم.
خیلی ممنون از این مقاله. حالا میدونم که برای رفع مشکل افت فشار باید به چه نکاتی توجه کنم.
این مقاله به من کمک کرد تا بفهمم که چرا هزینههای تولیدم رفته رفته افزایش پیدا کرده.
با توجه به این مقاله، به نظر میرسه که نگهداری منظم از دستگاه تزریق خیلی مهمه.
این مقاله به من یادآوری کرد که همیشه باید به فشار هیدرولیک دستگاه توجه داشته باشم.
فکر کنم یکی از دلایل افت فشار، تنظیم نبودن پارامترهای دستگاه باشه.
این مقاله به من کمک کرد تا با علل مختلف افت فشار آشنا بشم و بتونم مشکل دستگاه خودم رو تشخیص بدم.
خیلی خوبه که این مقاله راهکارهایی برای رفع مشکل افت فشار ارائه داده.
این مقاله به خوبی به بررسی عوامل مختلف موثر بر افت فشار پرداخته و اهمیت هر کدام رو توضیح داده.
با توجه به این مقاله، به نظر میرسه که طراحی قالب هم میتونه در ایجاد افت فشار تاثیرگذار باشه.
این مقاله به من یادآوری کرد که همیشه باید به وضعیت شیرهای اطمینان و فیلترهای دستگاه توجه داشته باشم.
این مقاله به خوبی توضیح داده که چرا افت فشار میتونه باعث کاهش کیفیت محصول نهایی بشه.
این مقاله به من کمک کرد تا بفهمم که چرا بعضی از مواد اولیه نسبت به مواد اولیه دیگه بیشتر باعث افت فشار میشن.
این مقاله به صورت جامع به بررسی عوامل فیزیکی و شیمیایی موثر بر افت فشار پرداخته و مدلهای ریاضی مرتبط رو هم معرفی کرده.
این مقاله به خوبی به بررسی تاثیر ویسکوزیته مواد مذاب بر افت فشار پرداخته و روشهای کاهش آن رو توضیح داده.
این مقاله به من کمک کرد تا بفهمم که چرا افت فشار در قسمتهای مختلف قالب متفاوت هست.
این مقاله به بررسی تاثیر دمای مواد مذاب بر افت فشار پرداخته و اهمیت کنترل دقیق دما رو توضیح داده.
این مقاله به من کمک کرد تا با روشهای مختلف اندازهگیری افت فشار آشنا بشم.